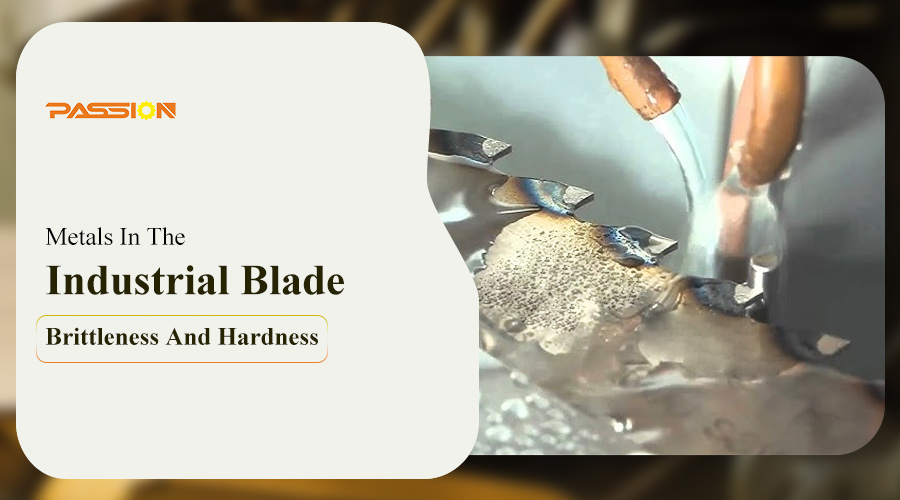
Sa industriya ng industriya, ang mga katangian ng mga metal ay pinakamahalaga. Ang katigasan, brittleness, katigasan at lakas ng isang talim ay may direktang epekto sa paggupit ng pagganap, buhay ng serbisyo at mga senaryo ng aplikasyon. Kabilang sa mga katangiang ito, ang ugnayan sa pagitan ng brittleness at tigas ay partikular na interes. Kaya, nangangahulugan ba ang mas mataas na brittleness na ang metal ay mas mahirap o mas marupok?
Ang Brittleness, bilang isang pisikal na pag -aari ng mga metal, ay nagpapahiwatig ng pagkahilig ng isang materyal na madaling masira kapag sumailalim sa mga panlabas na puwersa. Maglagay lamang, ang mga metal na may mataas na brittleness ay mas malamang na bali kapag sumailalim sa epekto o presyon. Ito ay katulad ng mga malutong na materyales tulad ng cast iron, na karaniwang matatagpuan sa ating pang -araw -araw na buhay, at kung saan ay may posibilidad na masira nang madali kapag sila ay sumailalim sa mga panlabas na puwersa.
Ang katigasan, gayunpaman, ay tumutukoy sa kakayahan ng isang materyal upang labanan ang isang matigas na bagay na pinindot sa ibabaw nito. Ito ay isa sa pinakamahalagang tagapagpahiwatig ng pagganap ng mga metal na materyales at karaniwang sinusukat sa mga tuntunin ng pamantayan tulad ng HRC, HV at HB. Sa larangan ng mga pang -industriya na blades, ang antas ng katigasan ay direktang tinutukoy ang kakayahan ng pagputol at pagsusuot ng paglaban ng talim. Ang mas mataas na katigasan, mas mahirap ang ibabaw ng talim ay dapat ma -scratched o matagos, na ginagawang mas angkop para sa pagputol ng mas mahirap na mga materyales.
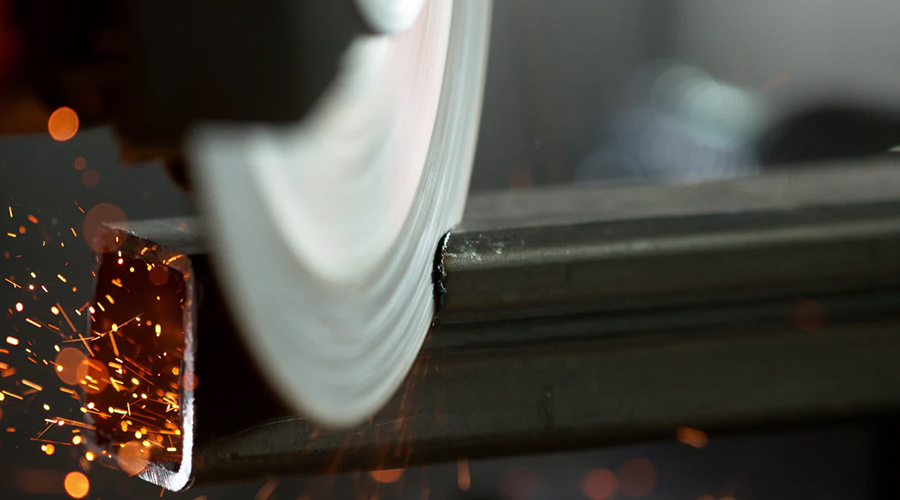
Kaya, mayroon bang hindi maiiwasang link sa pagitan ng Brittleness at katigasan? Sa isang paraan, ginagawa nito. Ang mga materyales na mas mahirap din ay karaniwang may mas malakas na mga bono sa pagitan ng mga atoms sa loob nito, na nagreresulta sa mga materyales na mas mahirap na mabago nang plastiko kapag sumailalim sa mga panlabas na puwersa at mas malamang na masira. Bilang isang resulta, ang mas mahirap na mga metal ay may posibilidad na maging mas malutong din.
Gayunpaman, hindi ito nangangahulugan na ang isang metal na may mataas na brittleness ay kinakailangang mas mahirap. Sa katunayan, ang katigasan at brittleness ay dalawang magkakaibang pisikal na dami, at walang direktang sanhi ng relasyon sa pagitan nila. Pangunahin ang tigas na sumasalamin sa kakayahan ng isang materyal na pigilan ang pagpindot sa labas ng mundo, habang ang pagiging brittleness ay mas salamin ng pagkahilig ng isang materyal na masira kapag sumailalim sa mga panlabas na puwersa.
Saindustriya ng talim ng industriya, Ang pagpili ng metal ay kailangang timbangin laban sa katigasan at brittleness depende sa tiyak na senaryo ng aplikasyon. Halimbawa, para sa mga blades na sumailalim sa mataas na bilis ng pagputol at mataas na temperatura na kapaligiran, ang mas mataas na katigasan at magsuot ng HSS o karbida ay madalas na pinili. Bagaman ang brittleness ng mga materyales na ito ay medyo mataas din, nagagawa nilang mapanatili ang mahusay na paggupit ng pagganap at buhay ng serbisyo sa ilalim ng mga tiyak na kondisyon ng pagputol.
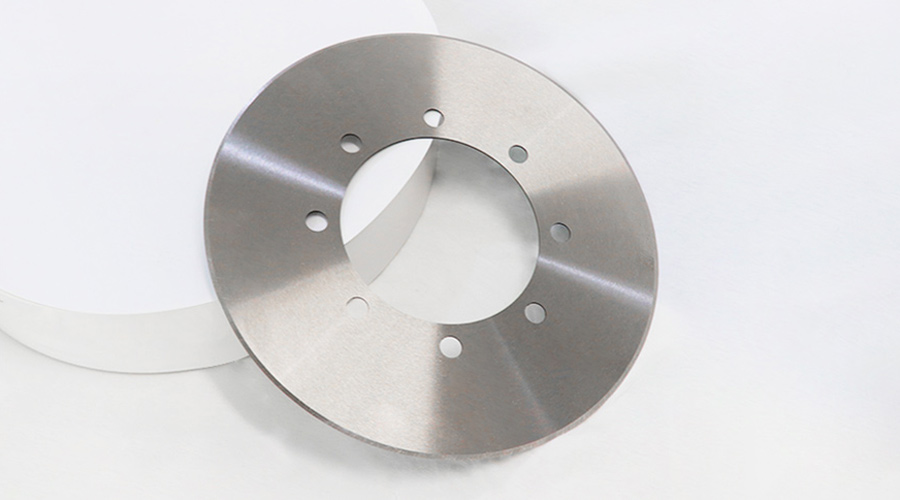
Para sa ilang mga blades na kailangang makatiis ng malaking puwersa ng epekto o kailangang baluktot nang paulit -ulit, tulad ng mga blades o gunting, kailangan mong pumili ng isang metal na may mas mahusay na katigasan at mas mababang brittleness. Titiyakin nito na ang talim ay hindi madaling masira kapag sumailalim sa mga panlabas na puwersa, sa gayon ay pinalawak ang buhay ng serbisyo nito.
Sa buod, ang ugnayan sa pagitan ng brittleness at tigas ay hindi lamang proporsyonal o inversely proporsyonal para sa mga metal sa industriya ng talim ng industriya. Kapag pumipili ng mga materyales sa talim, kinakailangan upang komprehensibong isaalang -alang ang mga katangian ng katigasan, brittleness, katigasan at lakas ayon sa mga tiyak na mga sitwasyon ng aplikasyon, upang makamit ang pinakamahusay na epekto ng paggupit at buhay ng serbisyo.
Kalaunan, magpapatuloy kaming mag -update ng impormasyon, at makakahanap ka ng karagdagang impormasyon sa aming website (Passiontool.com) blog.
Siyempre, maaari mo ring bigyang pansin ang aming opisyal na social media:
Oras ng Mag-post: DEC-06-2024